How to Choose Linear Displacement Sensor for Automation?
In automated systems, precision is the backbone of efficiency. From robotic arms positioning components to conveyor belts aligning products, accurate measurement of linear movement ensures processes run smoothly, reducing waste and minimizing errors. A linear displacement sensor is the critical component that provides this data, converting physical position into electrical signals that automation systems can act on. With a wide range of technologies—from potentiometers to laser sensors—choosing the right one for your automation setup requires careful consideration of your specific needs. Here’s a step-by-step guide to help you select the perfect linear displacement sensor.
Define Your Measurement Requirements
The first step in choosing a linear displacement sensor is to clarify the basic parameters of your application:
Measurement Range
Linear displacement sensors are designed for specific distance ranges, from sub-millimeter (for micro-automation, like semiconductor manufacturing) to several meters (for large-scale systems, such as industrial presses). Choosing a sensor with a range that matches your needs ensures accuracy—oversized ranges can reduce precision, while undersized ones may fail to capture full movement. For example, a robotic arm with a 500mm reach requires a sensor rated for 0–600mm (adding a 10% buffer to avoid maxing out the range).
Accuracy and Resolution
Accuracy (how close the measurement is to the true value) and resolution (the smallest change the sensor can detect) are non-negotiable in automation. For high-precision tasks like 3D printing or electronics assembly, a sensor with ±0.01mm accuracy and 0.001mm resolution is essential. For less critical applications—such as monitoring door openings in logistics—±0.5mm accuracy may suffice.
Keep in mind that environmental factors like temperature and vibration can degrade accuracy. If your automation system operates in harsh conditions, prioritize sensors with built-in compensation (e.g., temperature-stabilized components) to maintain precision.
Consider the Sensor Technology
Linear displacement sensors use various technologies, each with strengths and weaknesses. The right choice depends on your automation environment and requirements:
Potentiometric Sensors
These affordable sensors use a sliding contact on a resistive element to measure position. They work well for simple automation (e.g., basic material handling) but have limited accuracy (±0.5–1%) and a shorter lifespan due to mechanical wear. Avoid them for high-cycle applications (100,000+ movements) or clean rooms (where debris from wear is a concern).
Inductive Sensors
Inductive sensors detect metal targets without physical contact, making them ideal for dirty or high-vibration environments (e.g., automotive assembly lines). They offer good accuracy (±0.1–0.5mm) and long lifespans but only work with conductive materials. Use them to track the position of metal parts on conveyor belts.
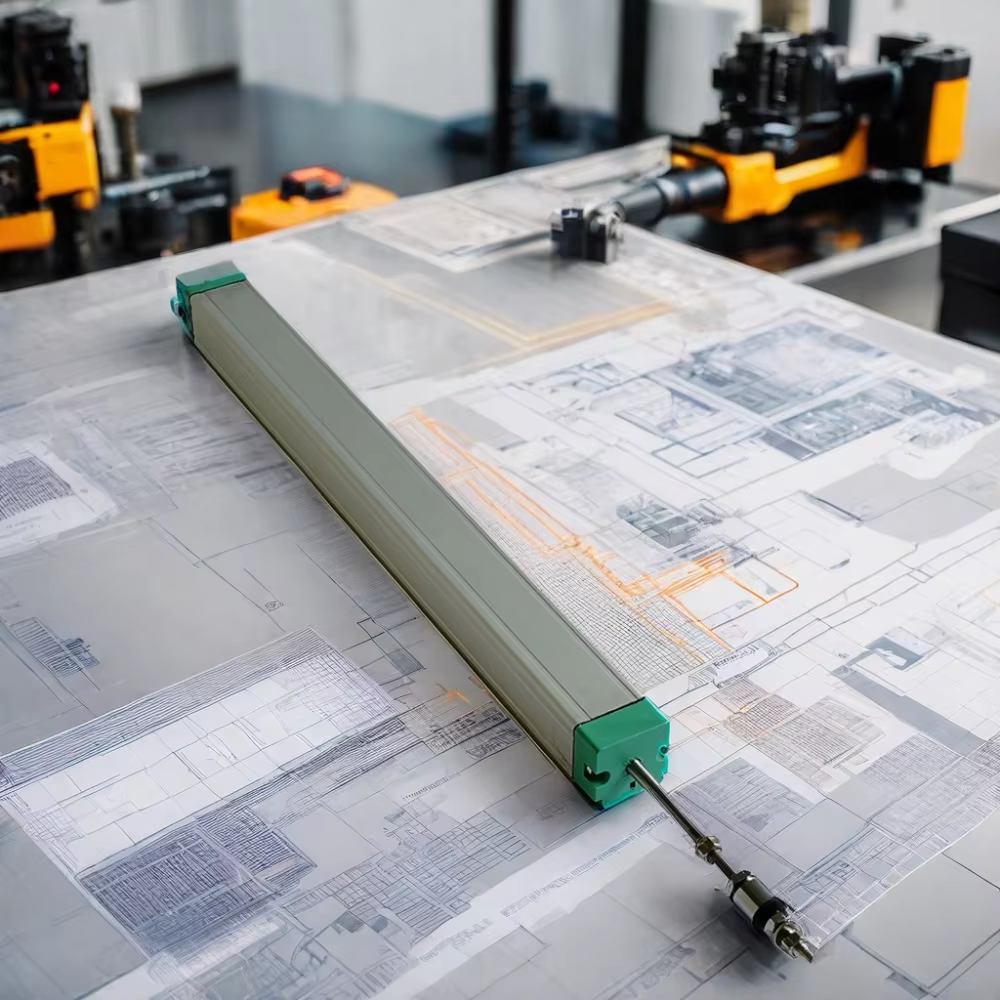
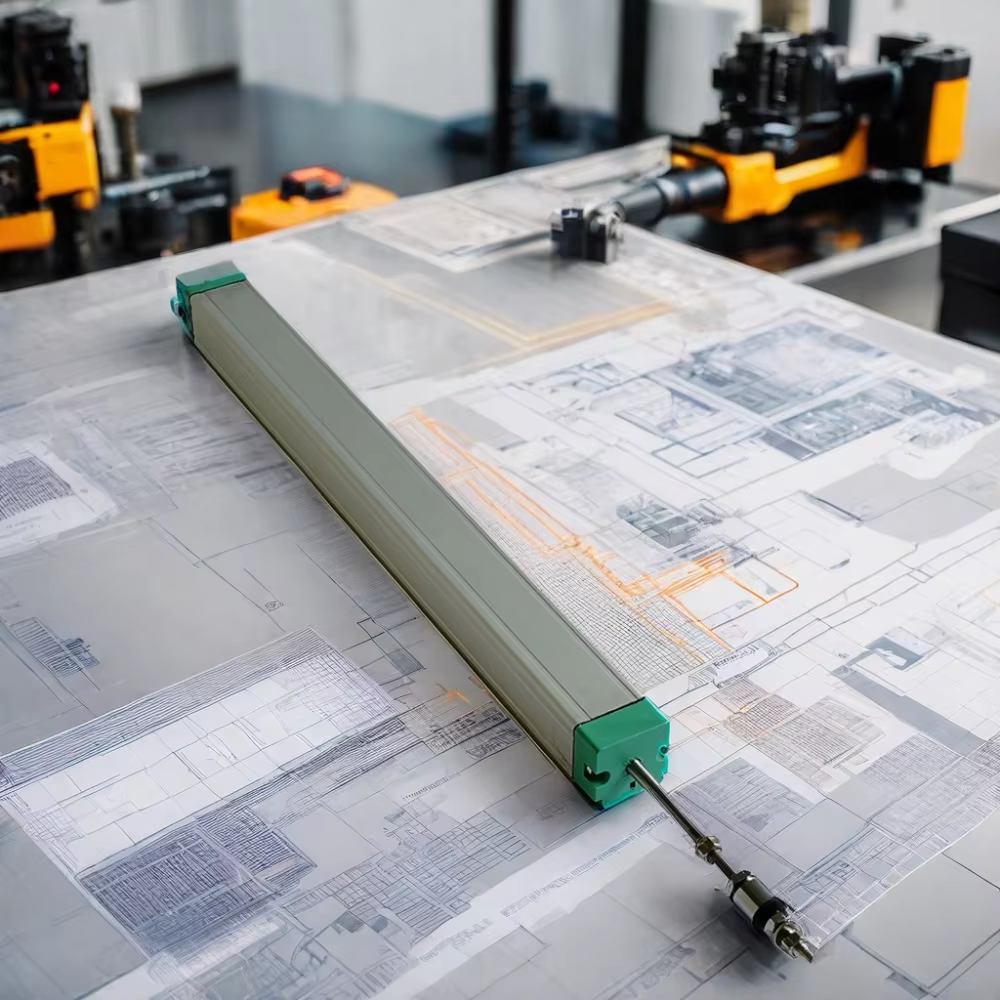
Capacitive Sensors
These sensors measure changes in capacitance between a probe and a target, working with both conductive and non-conductive materials (plastics, glass). They excel in cleanroom automation (semiconductor or pharmaceutical production) but are sensitive to humidity and dust, which can distort readings.
Optical Sensors (Laser or LED)
Optical linear displacement sensors use light to measure distance, offering high accuracy (±0.001–0.1mm) and non-contact operation. Laser models work over long ranges (up to 10m) and are suitable for precision automation, such as aligning solar panels. LED-based sensors are better for short ranges (up to 1m) and cost less than lasers. However, optical sensors struggle in dusty or smoky environments, which block light.
Magnetic Sensors
Magnetic linear displacement sensors use a magnet and Hall-effect sensor to detect position. They are rugged (resistant to oil, dirt, and vibration) and work in extreme temperatures (-40°C to 150°C), making them ideal for heavy machinery automation (e.g., mining equipment). Accuracy ranges from ±0.05–0.5mm, depending on the model.
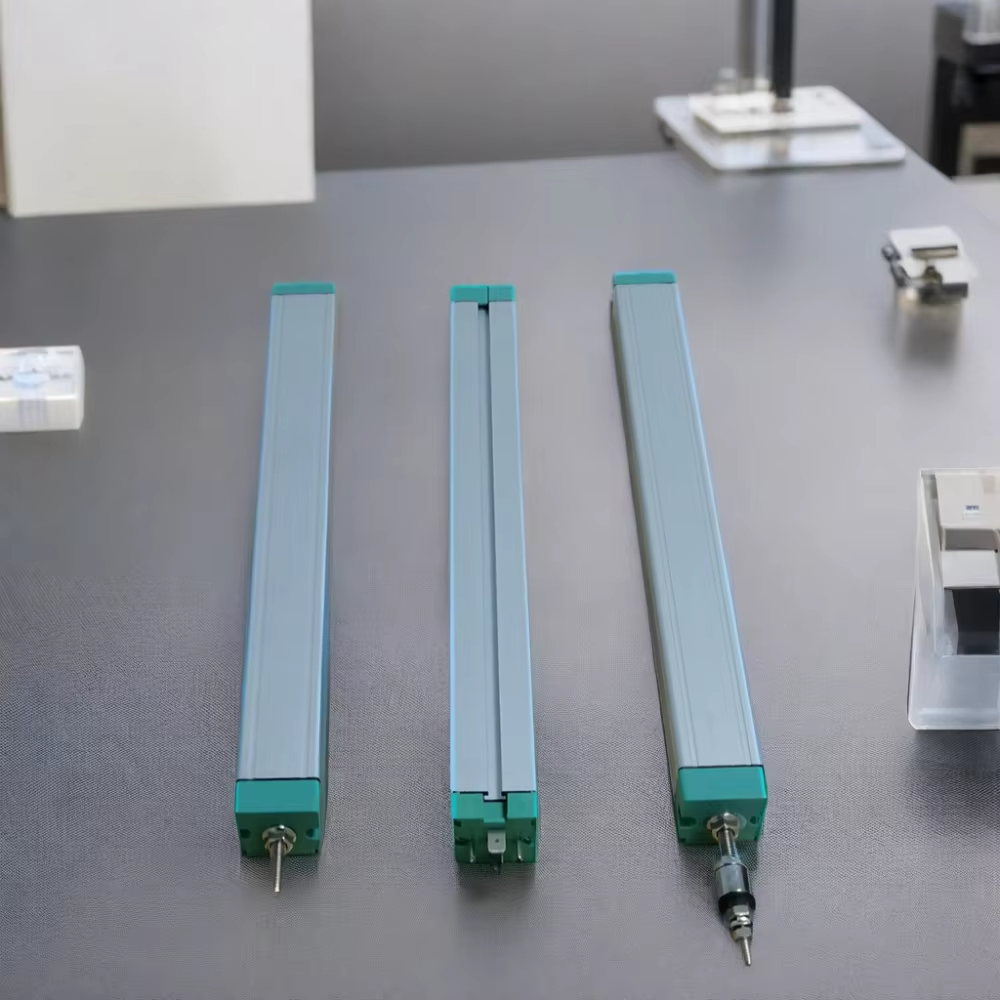
Draw Wire Sensors
As discussed in previous insights, draw wire sensors (a type of linear displacement sensor) use a cable to measure long ranges (up to 500m) with good accuracy (±0.1–0.5%). They are versatile for automation systems with large movements, such as crane positioning or telescopic arm control.
Evaluate Environmental Compatibility
Automation environments vary widely—from clean, temperature-controlled factories to dusty, outdoor industrial sites. A linear displacement sensor must withstand your specific conditions:
- Temperature: Choose sensors rated for your operating range. For example, food processing automation (with washdowns) needs sensors rated for 0–80°C, while foundries require models that handle 100°C+.
- Contamination: In dirty environments (e.g., metalworking), look for sensors with IP67 or IP68 ratings to resist dust and water. In cleanrooms, opt for non-outgassing materials (e.g., stainless steel) to avoid particle generation.
- Vibration and Shock: Industrial robots or heavy machinery produce vibrations that can disrupt sensitive sensors. Select models with vibration resistance (e.g., 10–2000 Hz) and shock ratings (e.g., 1000 G) to match your automation system.
- Electromagnetic Interference (EMI): Nearby motors or welders can cause EMI. Choose sensors with shielded cables and EMI-resistant electronics to ensure stable readings.
Check Output and Integration
A linear displacement sensor’s output must be compatible with your automation system (PLC, HMI, or robot controller). Common outputs include:
- Analog (0–10V, 4–20mA): Simple to integrate and suitable for most PLCs. Ideal for continuous monitoring (e.g., tracking a press’s position).
- Digital (RS485, Ethernet/IP): Offer faster data transmission and easier networking. Use them in smart automation systems where multiple sensors share data (e.g., a factory 4.0 setup with 10+ sensors).
- Pulse/Encoder: Provide incremental position data, useful for high-speed automation (e.g., sorting machines with moving belts).
Ensure the sensor’s response time matches your automation speed. For fast-moving parts (e.g., a bottling line with 100 bottles per minute), a sensor with a 1ms response time is necessary to avoid lag.
Factor in Installation and Maintenance
Ease of installation and maintenance reduces downtime in automation systems:
- Mounting Flexibility: Choose sensors with adjustable mounting brackets to simplify alignment. Some models offer wireless connectivity, eliminating cable routing issues in tight spaces.
- Calibration Needs: Sensors that require frequent calibration (e.g., some optical models) can disrupt automation. Look for “fit-and-forget” options with long-term stability (drift <0.1% per year).
- Replacement Accessibility: In hard-to-reach locations (e.g., inside a machine), select sensors with quick-disconnect cables and tool-free covers for easy replacement.
FAQ: Choosing Linear Displacement Sensors for Automation
What’s the difference between absolute and incremental linear displacement sensors?
Absolute sensors provide position data immediately (e.g., “500mm from home”), even after power loss. Incremental sensors measure changes from a starting point, requiring re-homing after power loss. Use absolute sensors for critical automation where downtime is costly.
Can I use a linear displacement sensor in a wet environment?
Yes—choose sensors with IP67/IP68 ratings. For submerged applications (e.g., water treatment automation), look for IP69K-rated models, which withstand high-pressure washdowns.
How do I ensure the sensor works with my PLC?
Check the sensor’s output (analog/digital) and voltage compatibility (e.g., 24V DC). Most manufacturers provide compatibility charts for major PLC brands (Siemens, Allen-Bradley).
What’s the best sensor for high-precision automation (±0.001mm)?
Optical laser sensors or capacitive sensors with sub-micron resolution. They work well for semiconductor or microelectronics automation, where tiny positional errors cause defects.
Are wireless linear displacement sensors reliable for automation?
Modern wireless sensors (using Bluetooth or LoRa) offer reliable performance for non-critical applications (e.g., warehouse rack monitoring). For high-speed or safety-critical automation (e.g., robotic welding), wired sensors are more stable.
Table of Contents
- How to Choose Linear Displacement Sensor for Automation?
- Define Your Measurement Requirements
- Consider the Sensor Technology
- Evaluate Environmental Compatibility
-
FAQ: Choosing Linear Displacement Sensors for Automation
- What’s the difference between absolute and incremental linear displacement sensors?
- Can I use a linear displacement sensor in a wet environment?
- How do I ensure the sensor works with my PLC?
- What’s the best sensor for high-precision automation (±0.001mm)?
- Are wireless linear displacement sensors reliable for automation?