Why Use LVDT Sensor for High-Precision Measurements?
In fields where precision is non-negotiable—from aerospace engineering to medical device manufacturing—measuring tiny linear displacements (as small as a few microns) demands a sensor that combines accuracy, stability, and reliability. Among the options, Linear Variable Differential Transformers (LVDTs) stand out as the gold standard for high-precision applications. Unlike potentiometers, optical sensors, or capacitive devices, LVDT sensors offer unique advantages that make them indispensable in scenarios where even a 0.1-micron error can compromise safety or functionality. Let’s explore why LVDT sensors are the top choice for high-precision measurements.
How LVDTs Work: A Design Built for Precision
LVDT sensors operate on electromagnetic induction, a principle that eliminates many sources of error found in mechanical or optical sensors. The core design consists of three components: a primary coil, two secondary coils (wound symmetrically around the primary), and a movable ferromagnetic core. When an alternating current (AC) is applied to the primary coil, it generates a magnetic field that induces voltages in the secondary coils. As the core moves linearly, the magnetic coupling between the primary and each secondary coil changes, causing the voltage in one secondary coil to increase while the other decreases. The difference between these voltages is proportional to the core’s position, providing a precise measurement of displacement.
This contactless design is key to the precision of LVDT sensors. Unlike potentiometers, which rely on sliding contacts that wear and introduce friction, LVDT sensors have no moving parts in contact—only the core floats within the coils. This eliminates mechanical wear, ensuring consistent performance over millions of cycles. The absence of friction also means the core can respond to even the smallest movements (as little as 0.01 microns), making LVDT sensors ideal for measuring micro-displacements in applications like atomic force microscopy or semiconductor wafer alignment.
Unmatched Accuracy and Linearity
High-precision measurements demand linearity—the ability to produce an output that is directly proportional to the true displacement. LVDT sensors excel here, with linearity errors as low as ±0.01% of full scale. For a LVDT sensor with a 10mm range, this translates to a maximum error of just 1 micron, a level of precision that optical sensors struggle to match in harsh environments.
This linearity is achieved through careful design in LVDT sensors: the secondary coils are wound to ensure symmetric coupling with the primary coil, and the core’s magnetic properties are optimized to minimize distortion. Advanced LVDT sensors also use signal conditioning electronics that compensate for temperature variations and power supply fluctuations, further reducing errors. For example, in aerospace applications—where LVDT sensors measure the deflection of aircraft wings—this level of linearity ensures that control systems receive accurate data, preventing instability.
Stability Over Time and Environment
High-precision measurements must remain consistent over extended periods and in challenging conditions. LVDT sensors are renowned for their long-term stability, with drift rates as low as 0.001% of full scale per year. This means a 10mm LVDT sensor will drift by less than 0.1 microns annually, far below the error tolerance of most high-precision systems.
Their stability stems from several factors in LVDT sensors:
- Robust Materials: Coils are wound with high-purity copper, and cores are made from nickel-iron alloys (e.g., Permalloy) that maintain magnetic properties over time. Housings are often stainless steel or Inconel, resisting corrosion and thermal expansion.
- Immunity to Environmental Noise: Unlike optical sensors, which are disrupted by dust or light interference, LVDT sensors are unaffected by contaminants. Their metallic construction also shields them from electromagnetic interference (EMI), a critical advantage in factories with nearby motors or welders.
- Wide Temperature Range: LVDT sensors operate reliably from -269°C (near absolute zero) to 200°C, with specialized models handling up to 600°C. This makes them suitable for high-precision measurements in cryogenic research or jet engine testing, where temperatures fluctuate drastically.
In medical device manufacturing—where LVDT sensors measure the movement of surgical robot arms—this stability ensures that procedures like laser eye surgery are performed with sub-micron accuracy, even after the sensor has been in use for years.
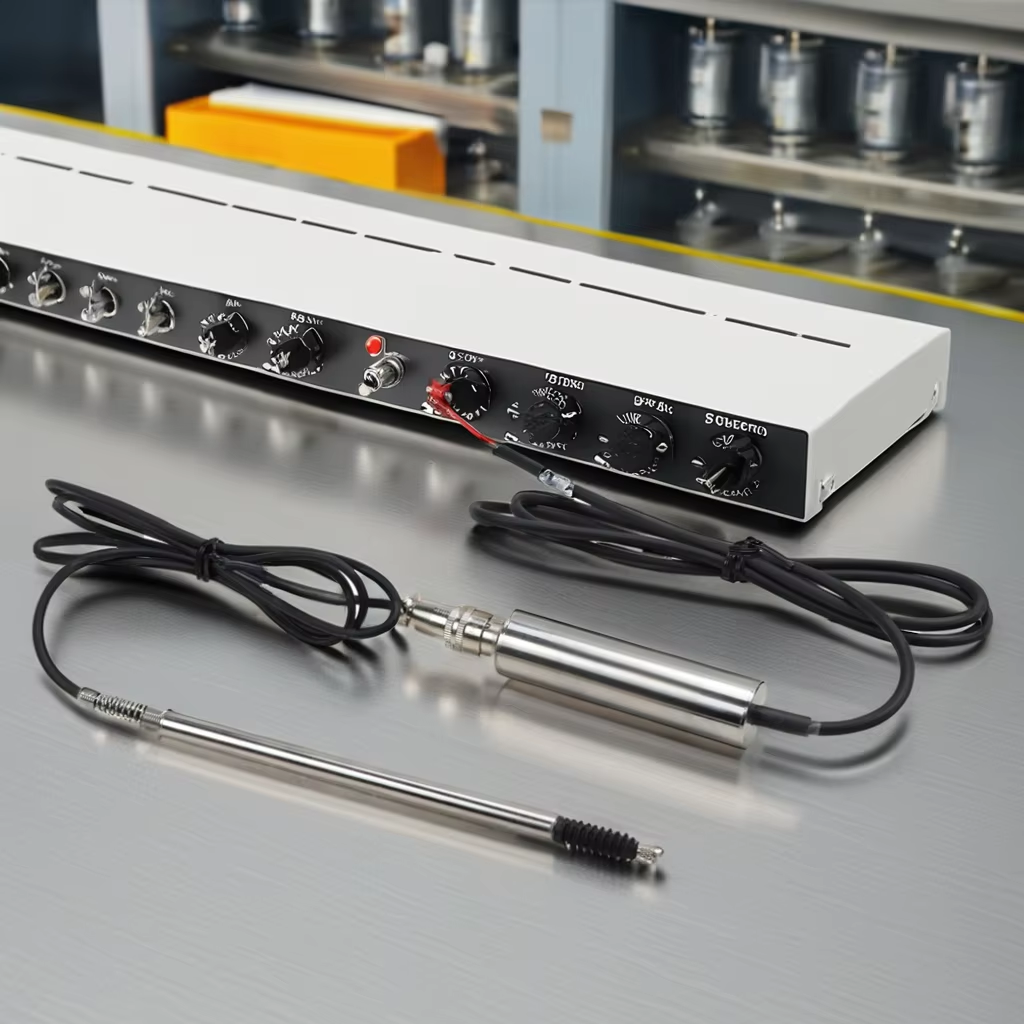
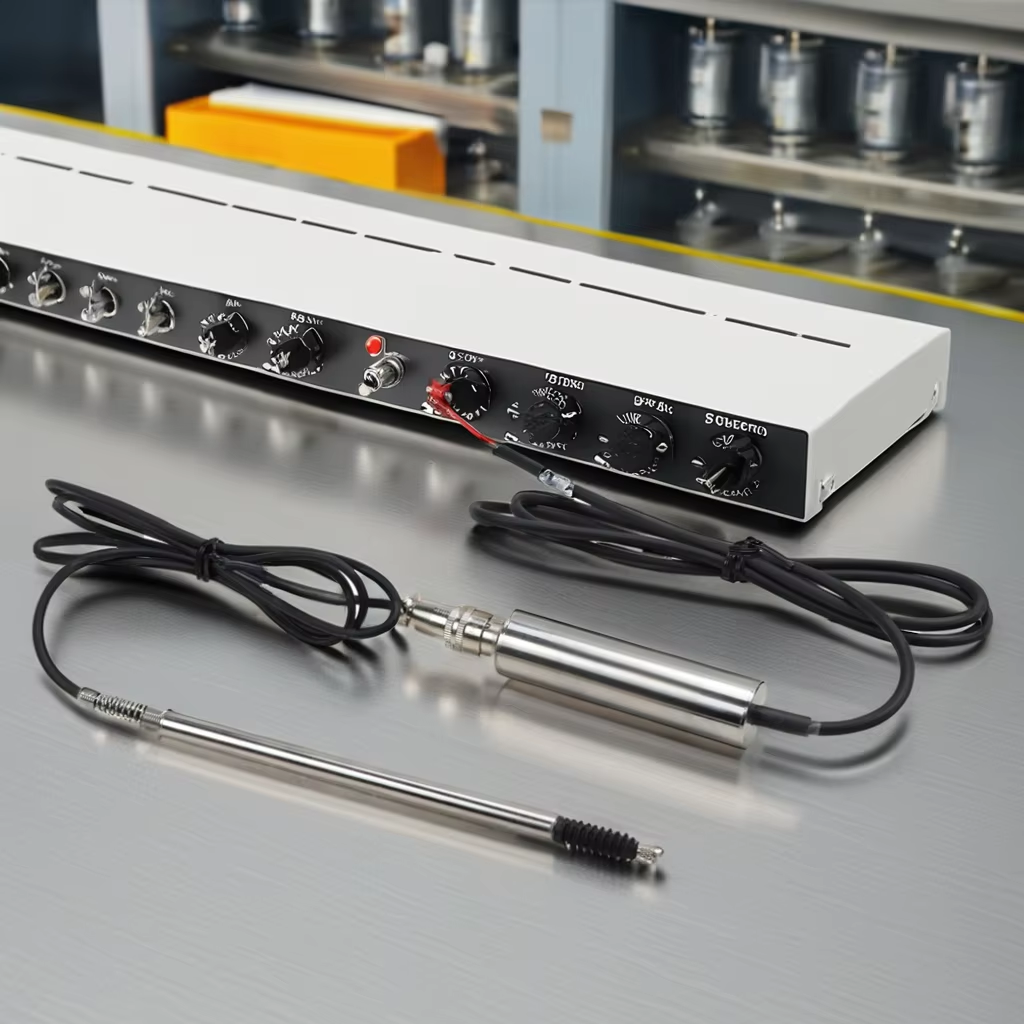
High Sensitivity to Small Displacements
Sensitivity—the ratio of output signal to displacement—is another area where LVDT sensors outperform many sensors. They can detect displacements as small as 0.001 microns (1 nanometer), making LVDT sensors ideal for applications like:
- Vibration Analysis: Measuring micro-movements in bridge structures to detect early signs of fatigue.
- Material Testing: Monitoring the expansion or contraction of materials under stress (e.g., testing the elasticity of carbon fiber composites).
- Nano-Manufacturing: Controlling the position of tools in semiconductor fabrication, where circuit features are just 5–10 nanometers wide.
LVDT sensors achieve this sensitivity by amplifying the differential voltage from the secondary coils. Modern signal conditioners in LVDT sensors convert this AC signal to a DC output with high gain, ensuring that even tiny core movements produce measurable voltages. This level of sensitivity is unmatched by potentiometers (limited by mechanical friction) or capacitive sensors (prone to noise in humid environments).
Versatility in High-Precision Applications
LVDT sensors are not limited to a single type of high-precision task—their design can be tailored to specific needs:
- Miniature LVDTs: With diameters as small as 2mm, these LVDT sensors fit into tight spaces like fuel injectors, where they measure valve lift with micro-meter precision.
- Spring-Loaded LVDTs: The core of these LVDT sensors is attached to a spring, ensuring constant contact with the target (e.g., measuring the thickness of ultra-thin films in battery production).
- Rotary Variants (RVDTs): While not linear, these variants of LVDT technology measure angular displacement with the same precision as LVDT sensors, making them useful for high-precision rotational applications like telescope positioning.
This versatility allows LVDT sensors to serve in industries from aerospace to nanotechnology, proving their adaptability to diverse high-precision needs.
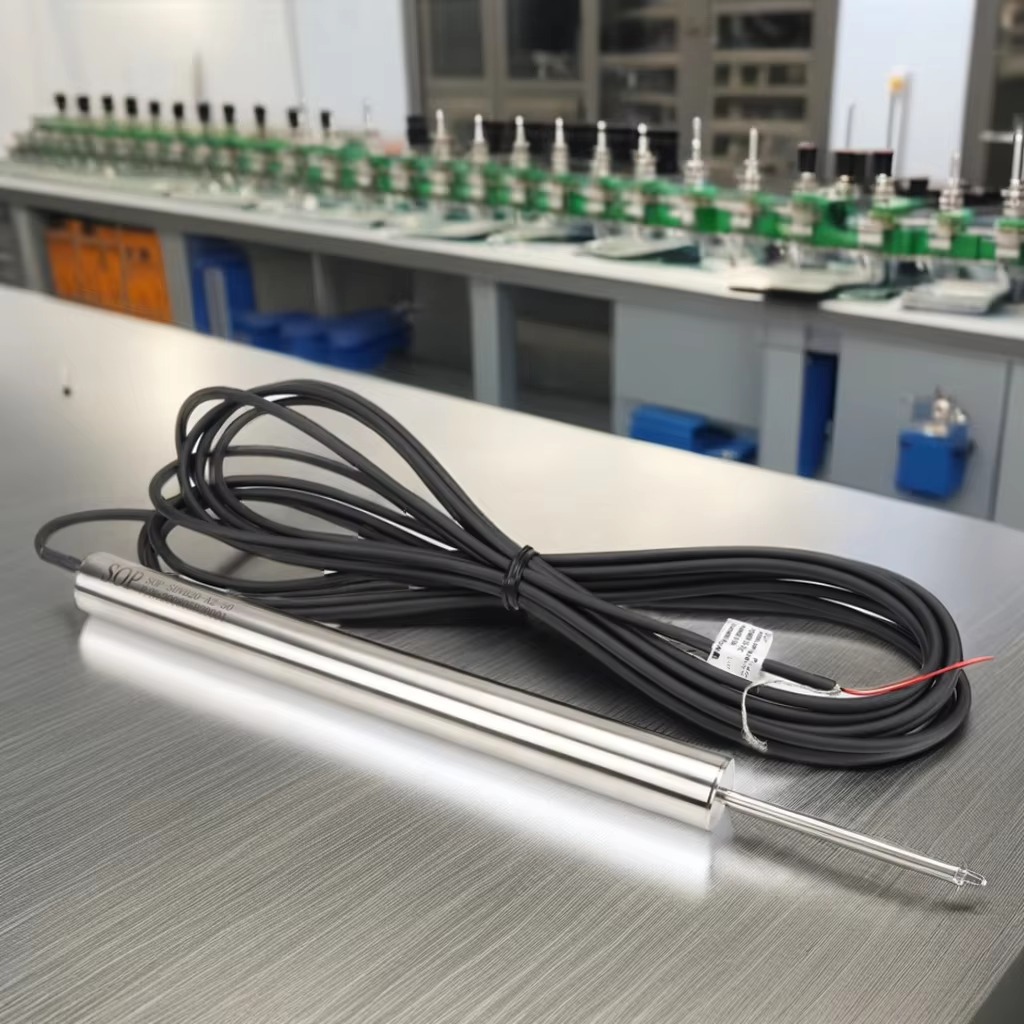
FAQ: LVDT Sensors for High-Precision Measurements
What is the typical range of an LVDT sensor?
LVDT sensors are available for ranges from ±0.1mm (200 microns total) to ±250mm, with high-precision models focusing on the smaller end (±0.1mm to ±10mm). Custom LVDT sensor designs can handle larger ranges while maintaining precision.
How do LVDT sensors compare to optical sensors in high-precision applications?
LVDT sensors offer better stability in harsh environments (dust, vibration, EMI) and have no moving parts to wear. Optical sensors may offer similar precision in clean, controlled settings but are less reliable in industrial or outdoor high-precision tasks where LVDT sensors thrive.
Can LVDT sensors measure dynamic (fast-moving) displacements?
Yes, but the response of LVDT sensors depends on the frequency of the AC excitation signal. Most LVDT sensors handle frequencies up to 10 kHz, suitable for measuring vibrations or fast movements in high-speed machinery (e.g., precision lathes).
Do LVDT sensors require regular calibration?
LVDT sensors are “fit-and-forget” sensors with minimal drift, so calibration is rarely needed. Most manufacturers recommend checking calibration of LVDT sensors every 1–2 years for critical applications, but this is far less frequent than for optical or capacitive sensors.
Are LVDT sensors compatible with digital automation systems?
Yes. Modern LVDT sensors include digital signal conditioners that output data via RS485, Ethernet/IP, or USB, integrating seamlessly with PLCs, data loggers, or computerized control systems in high-precision automation.